Modular, comfortable, with a refined aesthetic and sartorial details: a selection of furnishings designed to make every home interior truly unique
5 experimental materials for the future of design and architecture
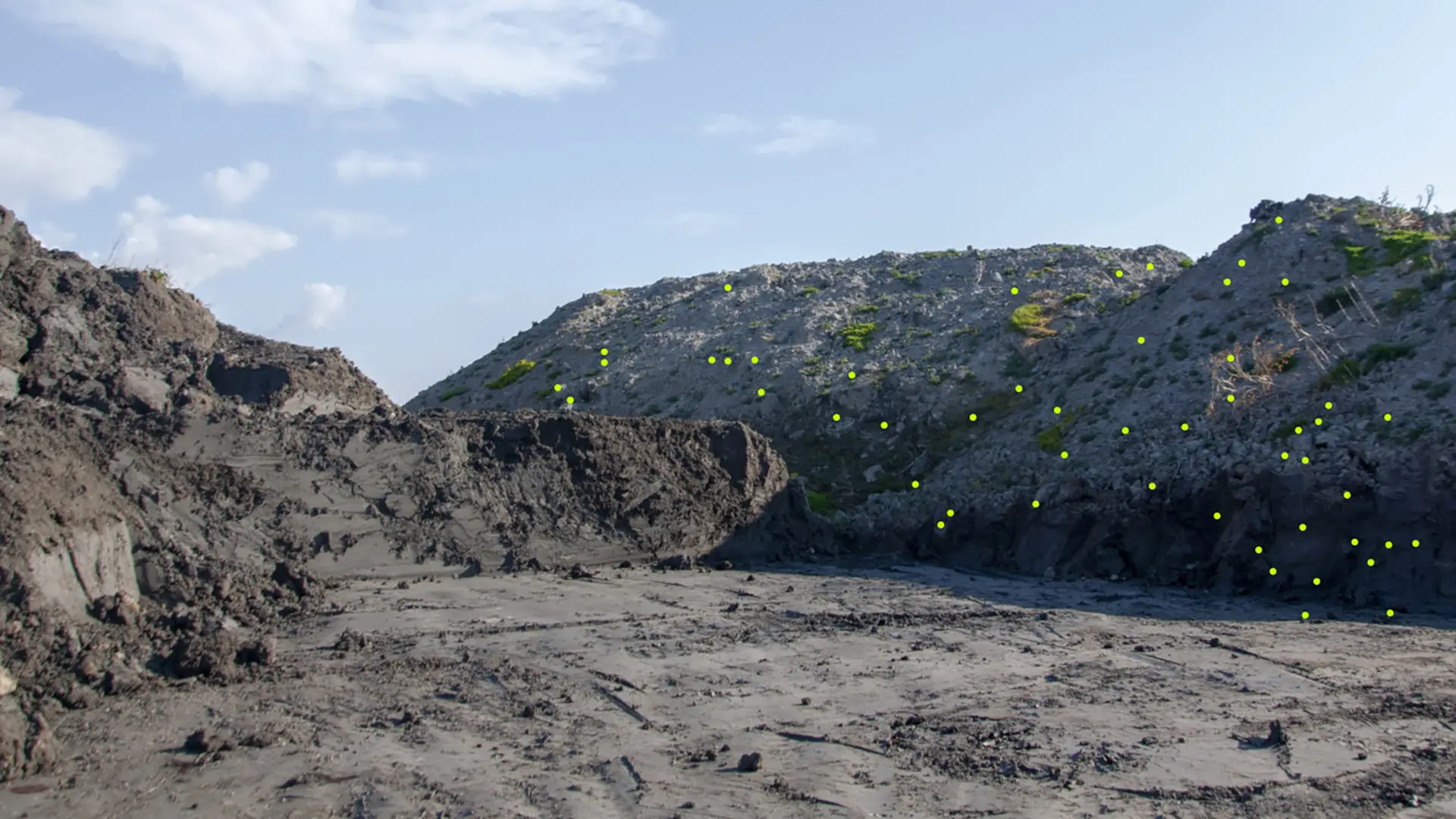
Turning polluted soil into bricks
A selection of material innovations for integration into buildings and products: micro-algae capable of absorbing CO2 like tall trees, fossil-free metals, photovoltaic membranes, bricks that sequester toxins from the land and biological textiles
Updated on 12 June 2023. There are many independent experimental research projects that could soon be harnessed at industrial level. These projects and glimmers of hope for sustainable development can help us imagine a future in which Man’s impact on the planet is significantly reduced.
PhotoSyntetica – CO2-absorbing micro-algae
Through the urban cultivation of micro-algae, EcoLogic Studio produces oxygen and reduces air pollutants. PhotoSyntetica is a research project that the London-based studio has been working on for several years, by means of a number of experiments, prototypes and installations that turn buildings into air pollution filters. The architects have developed a curtain that functions as a photobioreactor, in which a 2m2 module has the same efficiency as a tall tree. It combines the qualities of EFTE sheeting – a light, robust, translucent and chemically inert material – with the algae’s ability to capture solar radiation and absorb CO2 ten times more effectively than trees.
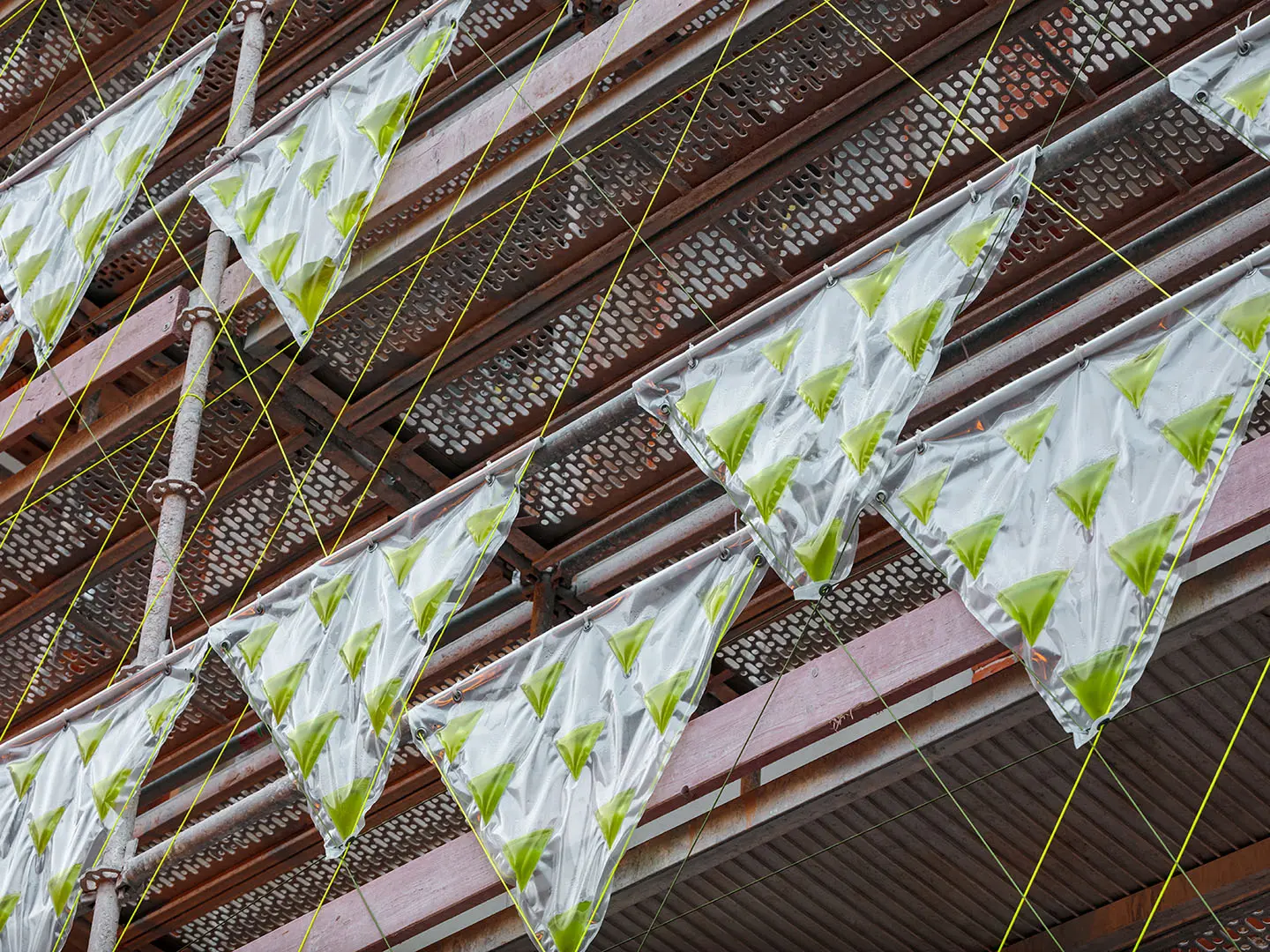
Ecologic Studio, PhotoSynthetica, urban curtains in Dublin and Helsinki. Ph Tuomas Uusheimo
AuREUS – photovoltaic film
The inventor of the AuREUS system garnered the first ever James Dyson Sustainability Award 2020 in the Sustainability category. It is a plastic material derived from agricultural waste that converts UV light into electric energy, developed by Carvey Ehren Maigue, an electrical engineering student at Mapua University in Manila. It is also very flexible and easy to use, as well as highly effective, regardless of weather conditions. Current tests indicate that it is capable of producing electricity 48% of the time, compared with 10-25% from photovoltaic cells. AuREUS has the merit not just of tackling one of the most pressing issues of our times – energy shortage – it could also potentially be used in different fields and by a large number of people.
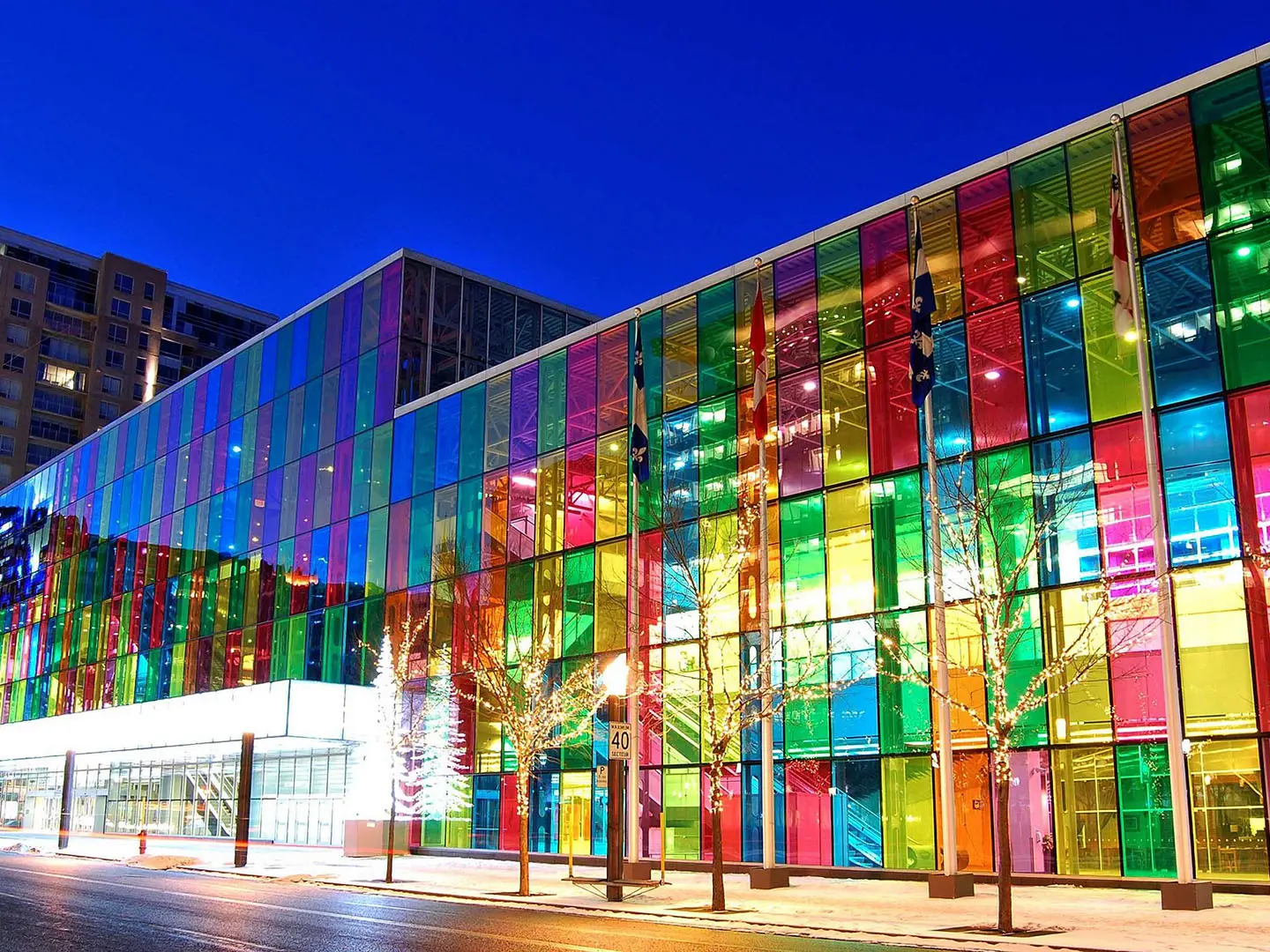
Carvey Ehren Maigue, AuREUS JDA Imagery Sustainability Winner
Claybens – bricks from polluted clay soil
Per- and polyfluoroalkyl substances (PFAS) are chemical products that are difficult to degrade. Used for decades in various industrial processes – textile production, electronics, paper coatings, paint, fire retardant foam and wax for skis – they persist at length in the environment and in the food chain. With her start up Claybens, Dutch designer Emy Bensorphas come up with a solution to the problem: heating PFAS contaminated clay soil to very high temperatures allows the chemical pollutants to be destroyed, creating a clean ceramic material. Claybens turns this into bricks that can be produced in bulk, allowing large quantities of soil to be cleansed rapidly.
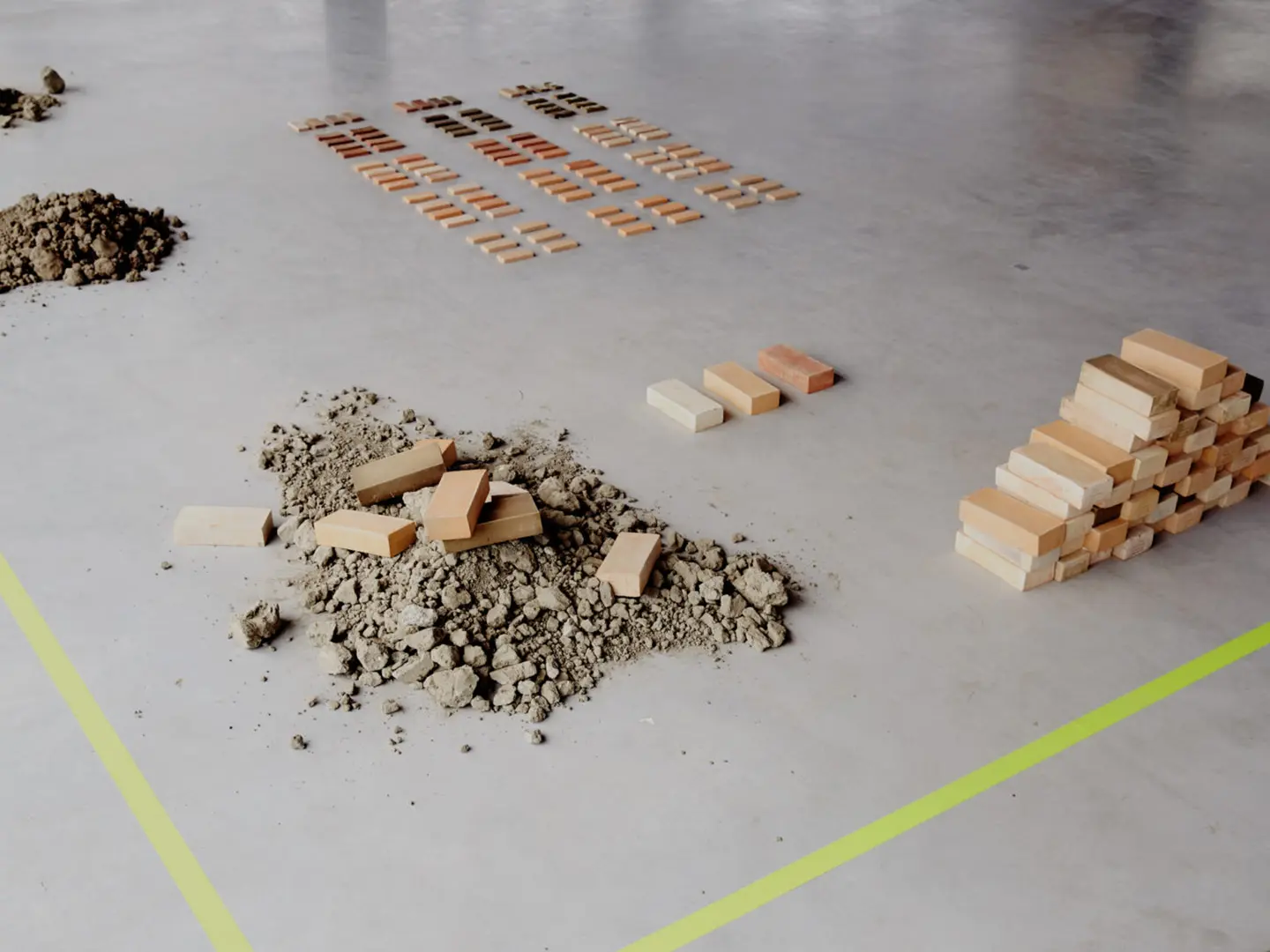
Turning polluted soil into bricks
HYBRIT – fossil-free steel
Steel is far from being considered a sustainable material. The industry that rotates around steel generates huge CO2 emissions - 1.85 tonnes of CO2 for every tonne of material produced. Between 12% and 14% of global CO2 emissions are associated with the steel industry. However, the Swedish firm SSAB Oxelösund has come up with what they say is the world’s first fossil-free steel, produced using green hydrogen rather than coking coal, by harnessing HYBRIT (Hydrogen Breakthrough Ironmaking Technology), created by the company along with LKAB and Vattenfall in 2016. Only small objects for demonstration purposes, such as a candlestick by the designer Lena Bergström have been produced thus far. The aim is to start using it in complex industrial processes over the next few years, and the Volvo Group is the company’s first large-scale client.